Automated Rolling Machine
Automation & Control was commissioned to create a new control board that could automate the tracking of an infeed roller angle to allow automatic centering of a tarpaulin.
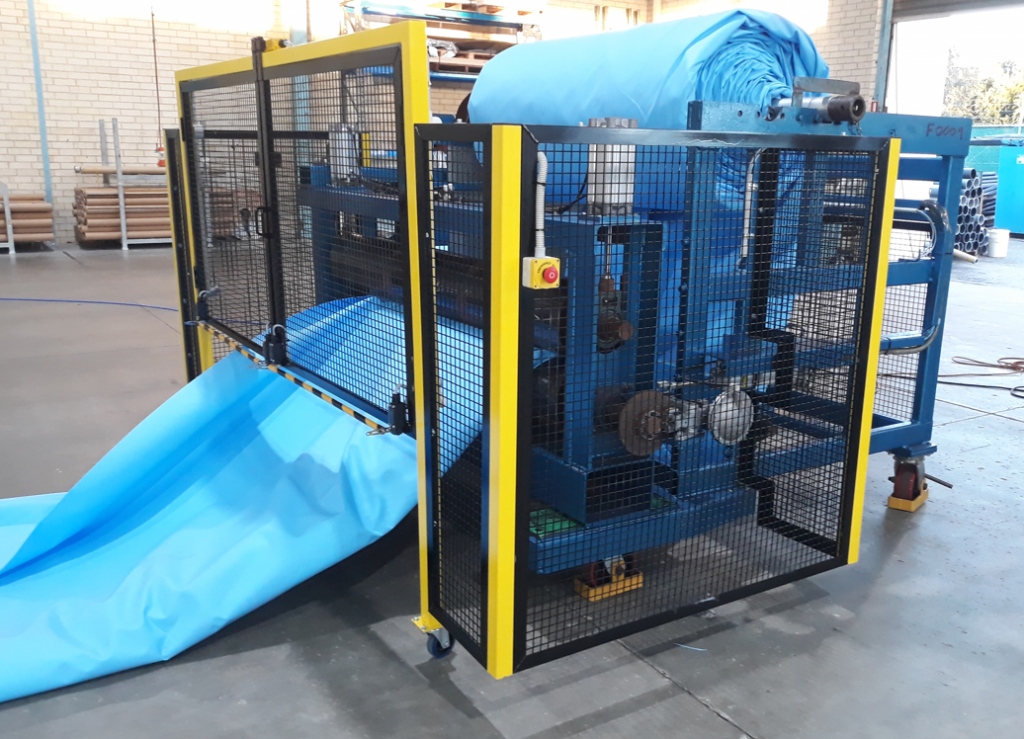
Our customer creates and joins large tarpaulin ground sheets which are used as lining for grain storage. The customer expressed great difficulty in folding and rolling the tarpaulin into tight compact rolls and keeping rolls centred on the coil. The client would have to allocate two employees to manually track the roll by forcing the tarpaulin left/right while driving it onto a roll and trying to maintain it being centred.
The customer wanted to develop a machine to drive a tarpaulin tight by incorporating a tensioning roller with brakes but also required safety elements as there was a potential hazard for operator entrapment and pinch points.
Project Requirements
To develop a machine, a new control board that would automate the tracking of the infeed roller angle to allow automatic centring of the tarpaulin while being driven onto the roll was needed.
As part of ensuring the safety operation of the machine, Automation & Control needed to design & build a safety system that would reduce the risk and hazards that the current machine presented.
Another factor of this project was the timeframe, our customer has peak seasons and required the completion of the machine to be fully operational prior to the start of the season to allow productivity gains.
Project Equipment
- New control system – PLC, Sensor monitoring and Analog Positioner Control
- New Safety System with 2 x safety bump levers, 3 estop push buttons and safety doors that are protected with guard switches.
Project Solution
Automation & Control used resources from MEG Group’s sister company, Techquip, who assisted by completing the welding and painting of the safety guarding which enabled Automation & Control to focus on the electrical system.
As a result, the machine was completed within the tight timeframe and now operates with one operator instead of the previous three operators (Two were previously required to continuously re-track the tarpaulin while being rolled).
Outcome
The machine is now a lot safer to use as direct access to any pinch points/ entrapment locations are isolated within the safety guarding/ safety system, improving OHS for the user.
The improvements to the machine have resulted in a 66% cost reduction for the client to roll a tarp. Traditionally this task took three staff to complete with two staff members manually guiding the moving tarp near the rotating roller. It is now completed efficiently by one person safely behind the new guarding away from pinch points and entrapment locations.
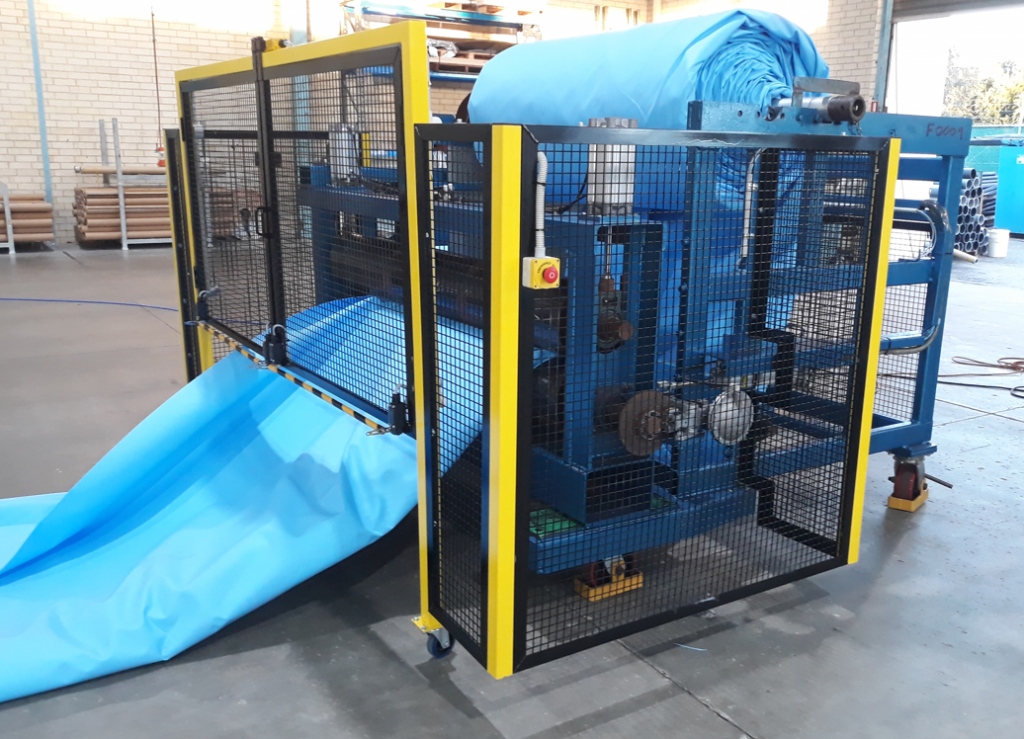
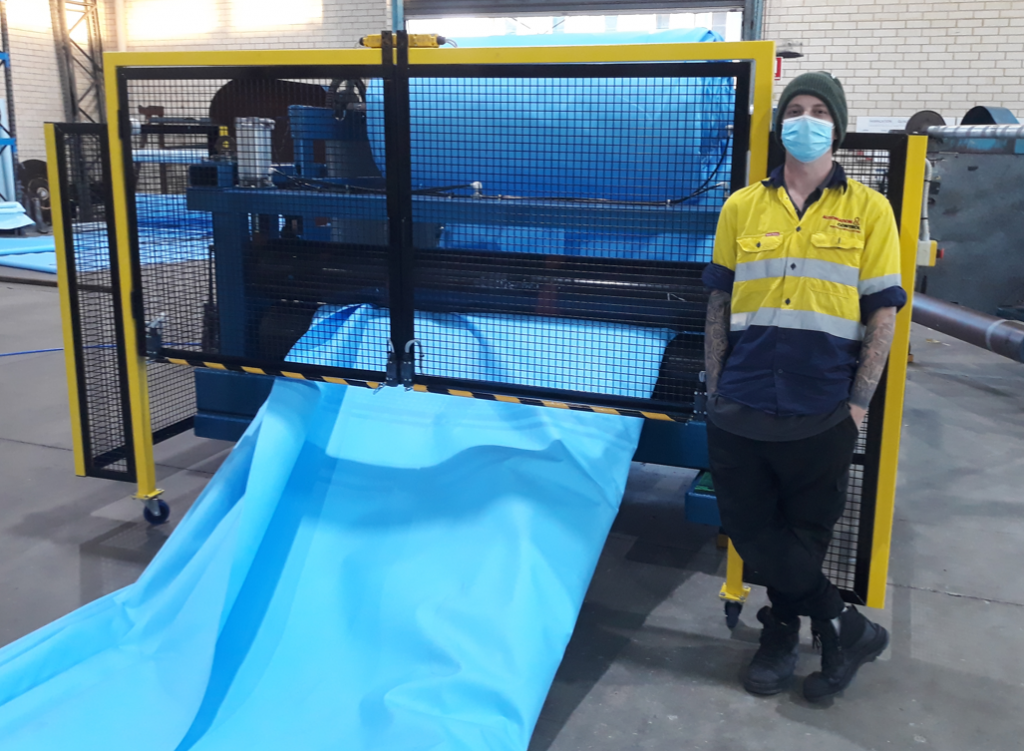