Modu Gripper Conveyors
Elevator / Lowerator, available in four main types including C-Flow, Simple Gripper Upender, Gripper Upender and S-Flow.
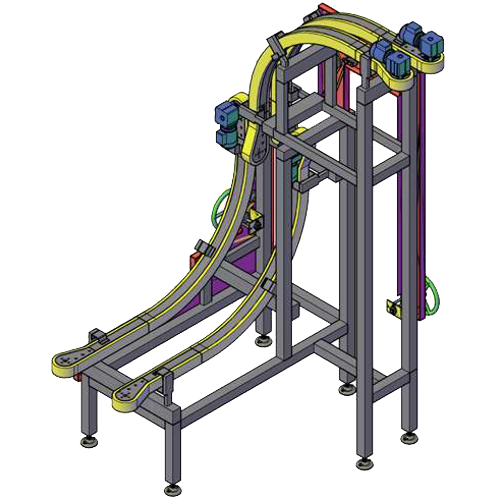
A gripper is utilised for moving the products up and down or to put things on a hold between the conveyers or at the finishing stage of the conveyor. Two sets of conveyors are attached in a gripper in order to transport products to higher or lower elevations while taking up minimal floor space. It holds the product in a firm but gentle manner before releasing it to another conveyor.
A Gripper Conveyor has many uses; it can be used to elevate products, lower products, or buffer products. It consists of two parallel sets of conveyor sections that are joined together on an adjustable mechanism which allows the unit to accommodate different size products. The Gripper unit can be configured to allow the product to be transferred at the same or different input/output transfer heights. The unit gently grips the product to be transferred and guides it to the next process.
The Gripper Conveyor offer product elevation, de-puck & reverting, creates passage ways, allows for inverter air rinsing and change orientation solutions.
Product range
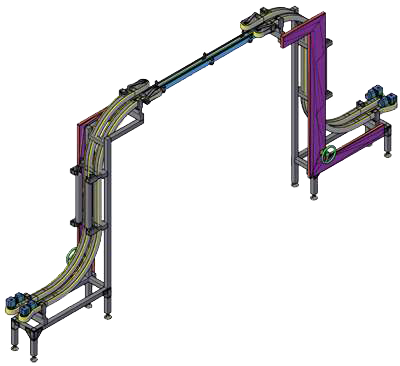
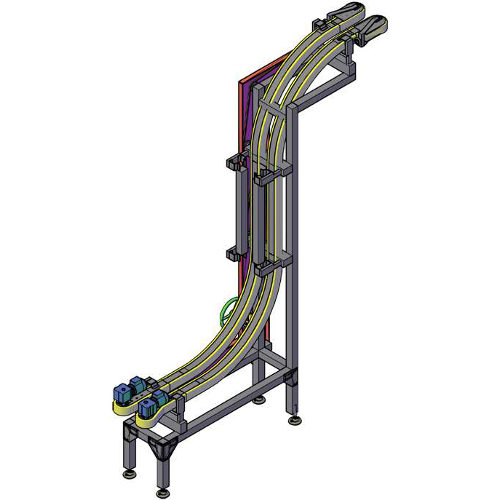
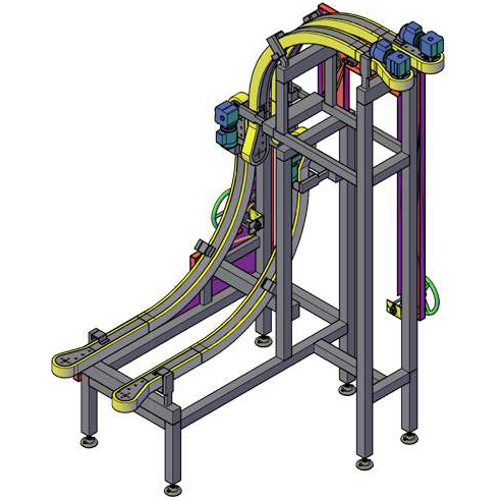
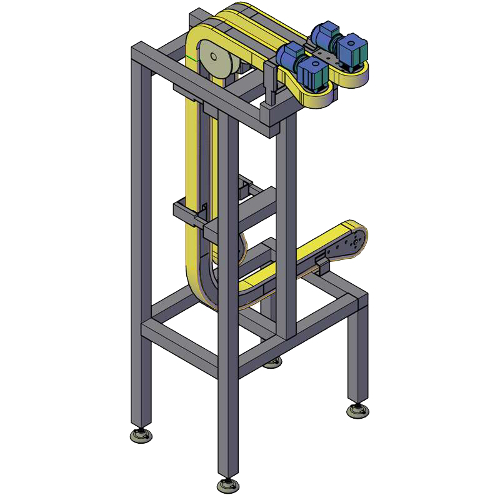
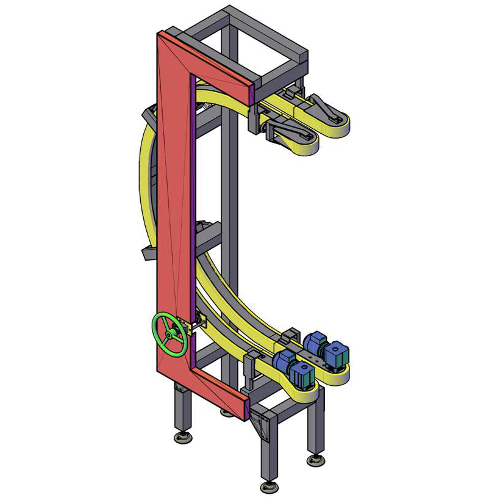
Features
- Saves floor space and conveyor length
- Maximize space utilization by creating buffering at ceiling levels.
- Easily integrates with other application such as blowers, fillers, and packaging lines
- Flexible and lightweight
- Easy to install and accommodate site layouts.
- High capacity vertical transport
1. Product Elevation Gripper conveyers picks up items from an in-feed conveyor, transports them to a higher or lower level elevation, and releases them for a discharge conveyor. The discharge end is utilized for placing the drives. Gripper conveyor is ideal for palletizing, filling, packing, buffering, blowing, etc. |
2. Change Orientation Gripper upended design alters the product placement by 90º. Gripper conveyer collect items from an in-feed conveyor, transports them to a higher or lower level elevation, and releases them for a discharge conveyor. The discharge end is utilized for placing the drives. |
3. Product De-Puck A basic de-pucking system could be realized by installing a short gripper conveyor on top of plain chain conveyor. The bottles that have been already filled are detached from puck when entering gripper conveyor and transferred to another conveyor for capping process while the puck is returned to the initial point in order to fill empty bottles. |
4. Product Reverting Lifts items from an in-feed conveyor, inverts product orientation, and releases them on to a discharge conveyor. The discharge end is utilized for placing the drives. Prior to entering filling machine, Product reverting conveyor is utilized for cleaning and drying. |
5. Creating Passage Way Lifts items from a horizontal in-feed conveyor, transports the product above a reasonable height at a short distance, then lowers and levels out to release them to a horizontal discharge conveyor, allowing enough access for the operator or fork lifter from each side. |
6. Inverter Air Rinser Lifts products from a horizontal in-feed conveyor, topples them at an angle of 180º, transports them through an air cleaning or air cleaning/ionizing sector (or any other category of specific process or equipment as defined by the customer), topples them back to their original angle and releases them to horizontal discharge conveyor. |
Resources
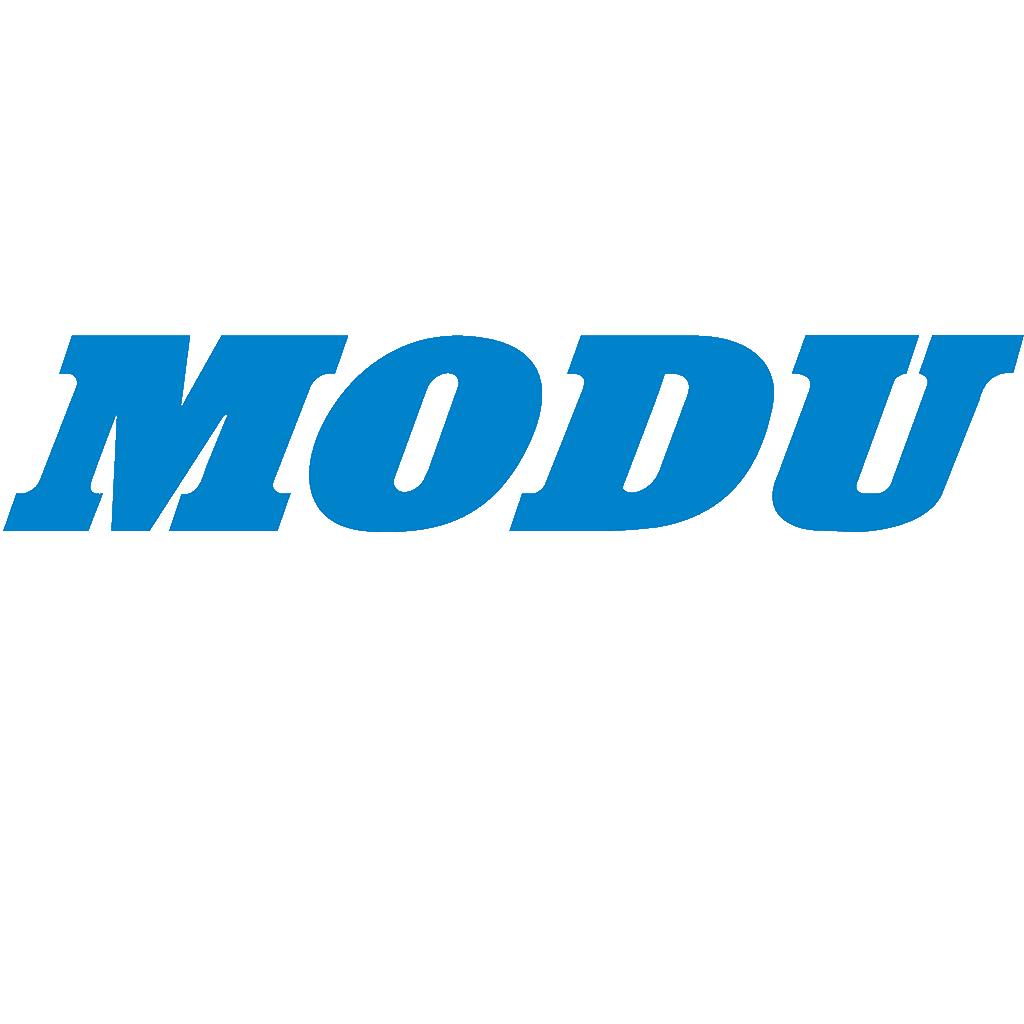