Comau N-220 Robot
An innovative architectural approach based on an intensive use of modularity as well as components reduction, compact motors and new control drivers.
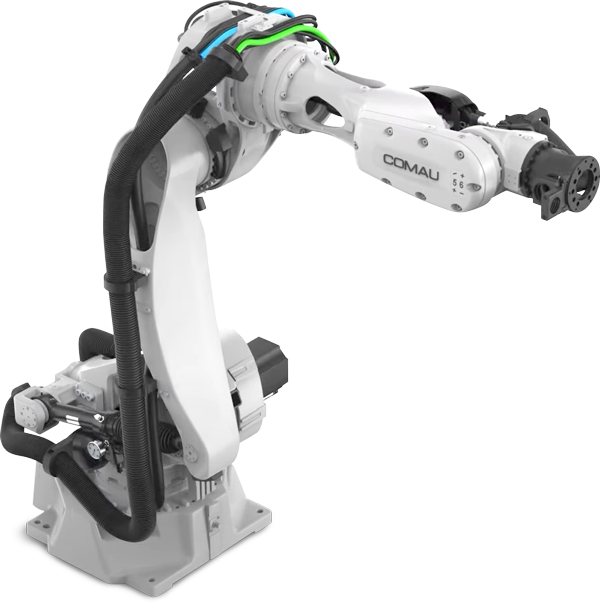
Lower your cost of production by increasing company’s levels of quality and supply chain flexibility, while ensuring straightforward integration.
We can offer you advanced technology directly from Comau’s Innovation Center of Advanced Robotics in Turin (Italy).
The most evolved motion algorithms are now suitable with Comau e-Motion 3.0 to provide excellent performances both in terms of cycle time, repeatability and path control accuracy: it is suitable for spot welding and material handling applications, as well as for continuous processing like 3d printing and gluing.
With its wide working area and Performance Level D cartesian safety features, the high payload (220 kg) robot is perfect for a vast range of industries including automotive, food & beverage, fulfillment and logistics, among others.
N-220 robot is supplied in a basic dressing with multibus cable and air hose up to ax 3, to which it is optionally possible to combine an easy dressing solution with a corrugated hose within the hollow forearm, up to axis 5 of the robot.
Easy integration
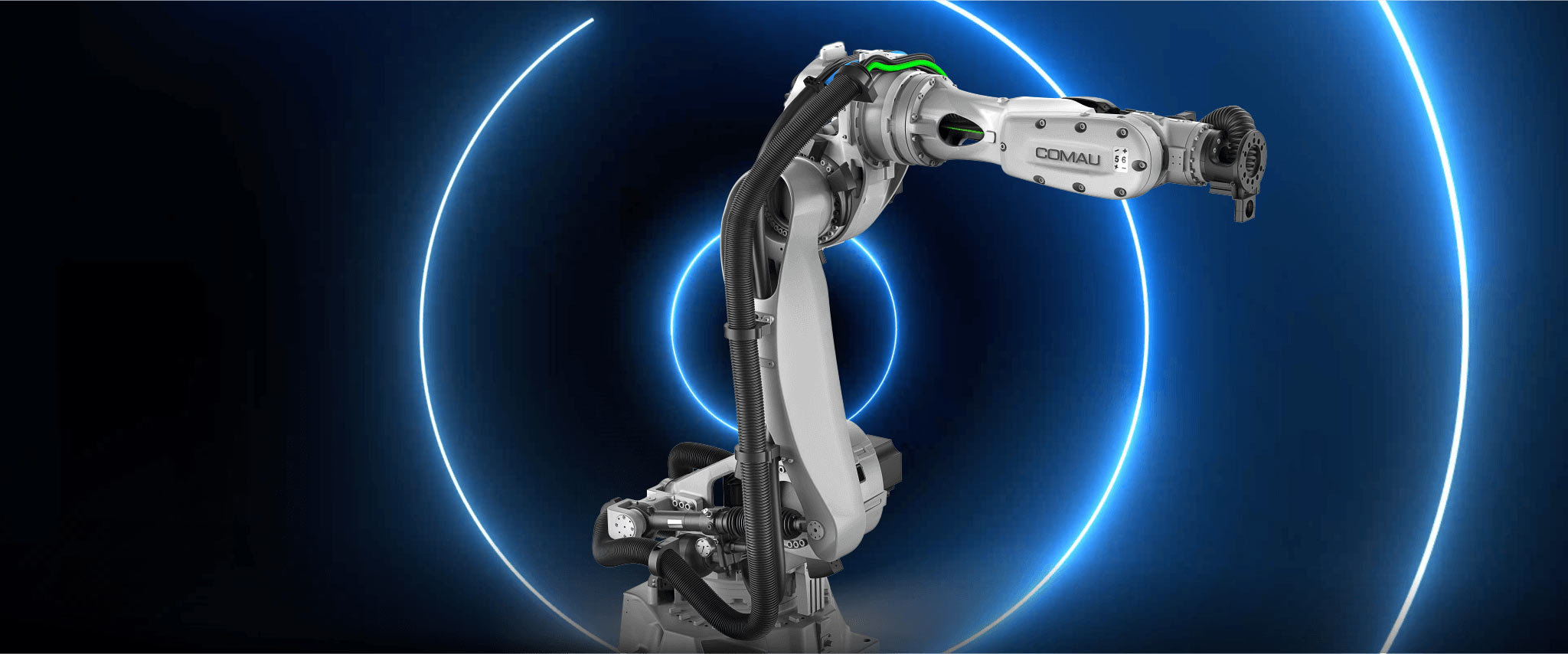
& hytorc option ready for automatic base tightening.
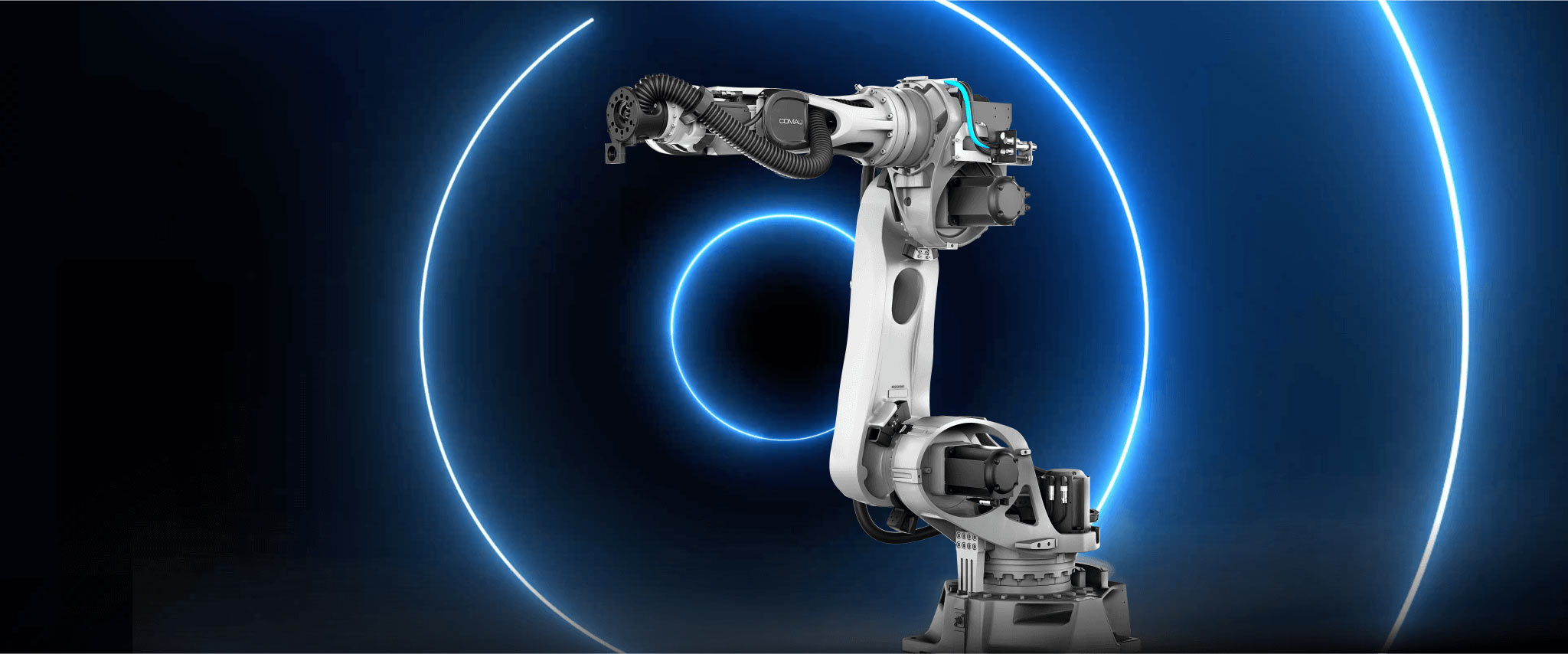
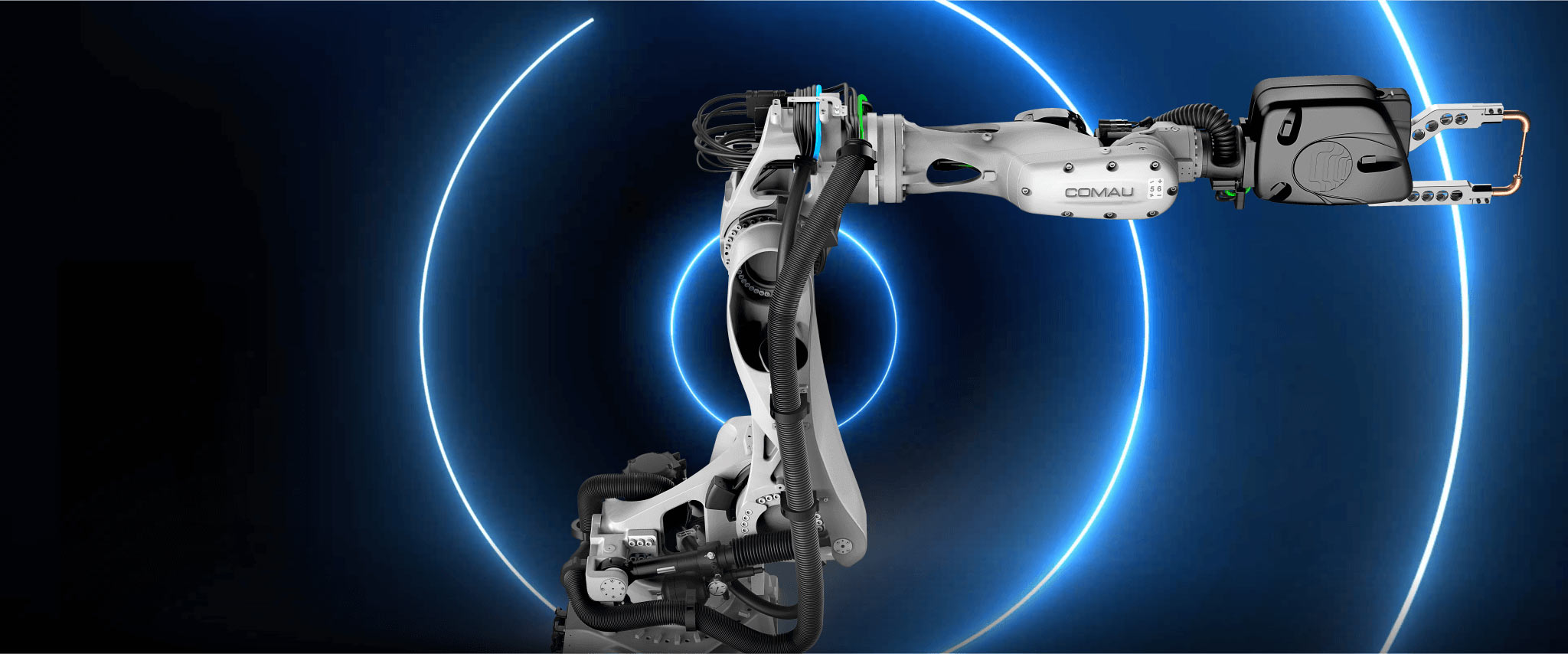
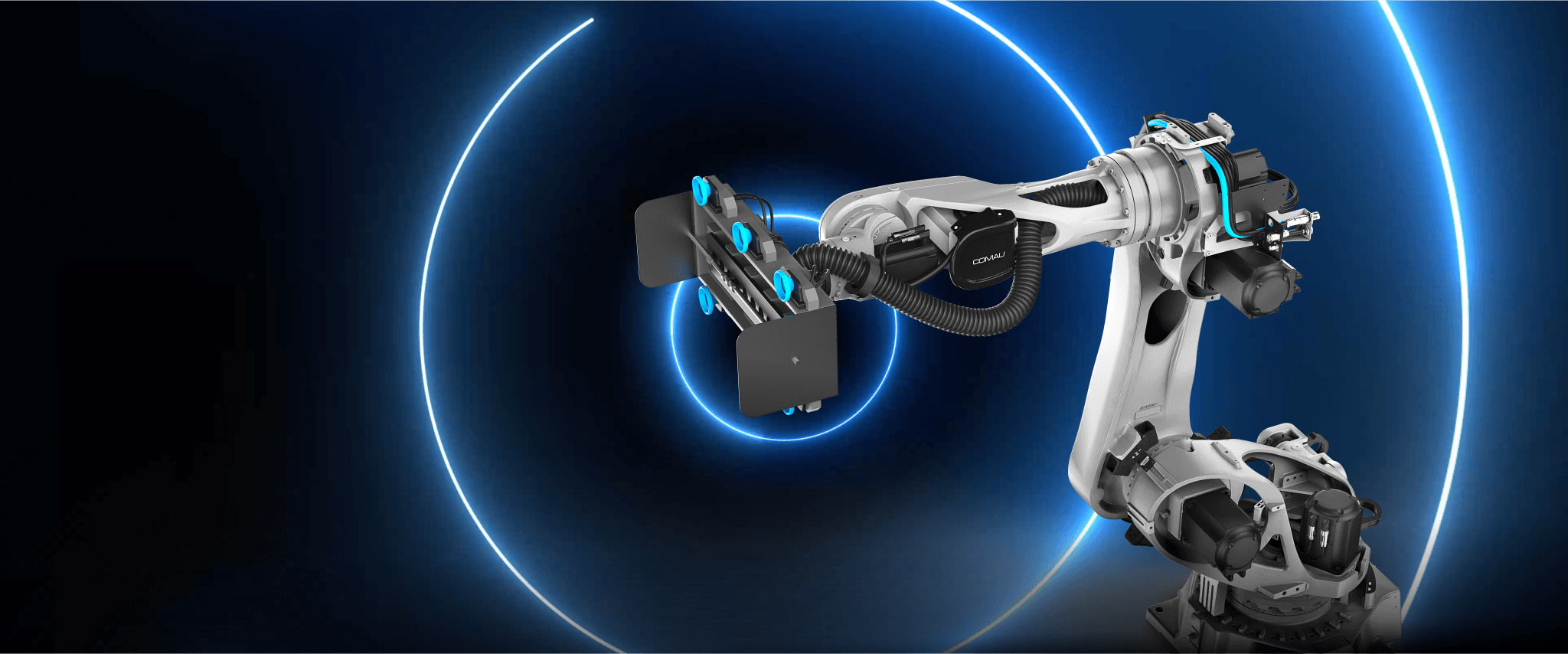
Watch COMAU N-220 Robot video
Features
- Direct assembly between motor and gearbox
- Visual recalibration for “turn-set” recovery
- Enhanced SW motion algorithm with e-Motion 3.0
- Wide working areas
- Improved MTBF and lower MTTR
- Multiarm programs
- IoT ready, MES compliant, Field availability, OPC UA
- Safe Motion and Safety Bus Options available
Benefits
- Excellent performance in terms of cycle time, repeatability and path control accuracy
- The significant reduction in components lowers supply chain risks
- Easy to use, easy to integrate and easy to maintain
- Improves total cost of operation and optimizes Mean Time To Repair (MTTR)
- Powerful, cost-effective automation
- Perfect for spot welding and material handling applications, as well as for continuous processing like 3d printing and gluing
Working areas
The use of a balancing system with nitrogen for axis2 (and larger axis3 stroke-ends) allow N-robot a wide backwards working area: that is ideal for bending and agile handling applications.
Technical data sheet N-220 robot
Model | N-220-2.7 |
Number of axes | 6 |
Maximum wrist payload | 220 kg |
Additional load on forearm | 50 kg |
Maximum horizontal reach | 2670 mm |
Torque on axis 4 | 1270 Nm |
Torque on axis 5 | 1270 Nm |
Torque on axis 6 | 780 Nm |
Stroke / Speed Axis 1 | +/- 180° (120° / s) |
Stroke / Speed Axis 2 | -77° / +76° (100° / s) |
Stroke / Speed Axis 3 | -167° / +74° (110° / s) |
Stroke / Speed Axis 4 | +/- 200° (140° / s) |
Stroke / Speed Axis 5 | +/- 125° (140° / s) |
Stroke / Speed Axis 6 | +/- 2700° (210° / s) |
Repeatability | 0.05 mm |
Tool coupling flange ISO | 9409 – 1 – A 125 |
Robot weight | 1193 kg |
Protection class | IP65 |
Mounting position | Floor |
Operating area type | Type 1 |
Operating areas A | 3076,4 mm |
Operating areas B | 2670,5 mm |
Operating areas C | 1850,0 mm |
Operating areas D | 1552,2 mm |
Operating areas E | 222,7 mm |
Operating areas F | – |
Control | C5G Plus Rel.3 |
Dimensions: | 3800x1110x510 mm |
Weight: | 125 kg |
Working temperature: | 5 to 45°C (5 to 55°C with cooler) |
Humidity: | from 5% to 95% without condensation |
Extended line power range: | 400 to 500V |
Available for: | N-220 |
SAFE Control: | available version |
Servo-gun ready | available version |
Resources
Other Comau Products
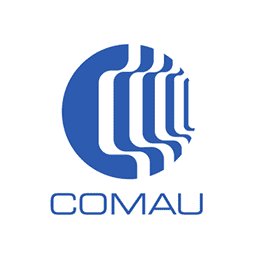